In recent years, 3D printing has emerged as a groundbreaking innovation worldwide, offering immense potential in various sectors, including engine technology and the construction of houses and buildings. India, a fast-growing technology hub, is gradually adopting this advanced manufacturing process to enhance its industrial landscape, improve efficiency, and cut costs. This shift could propel the nation into a leadership position in sustainable and innovative technologies.
What is 3D Printing?
3D printing, also known as additive manufacturing, is a process that involves creating three-dimensional objects from a digital model. This technology builds objects layer by layer using materials such as plastic, metal, or concrete, enabling the production of highly complex structures that would otherwise be challenging or costly to make using traditional manufacturing techniques. As the technology continues to evolve, its applications in India are expanding rapidly across various industries.
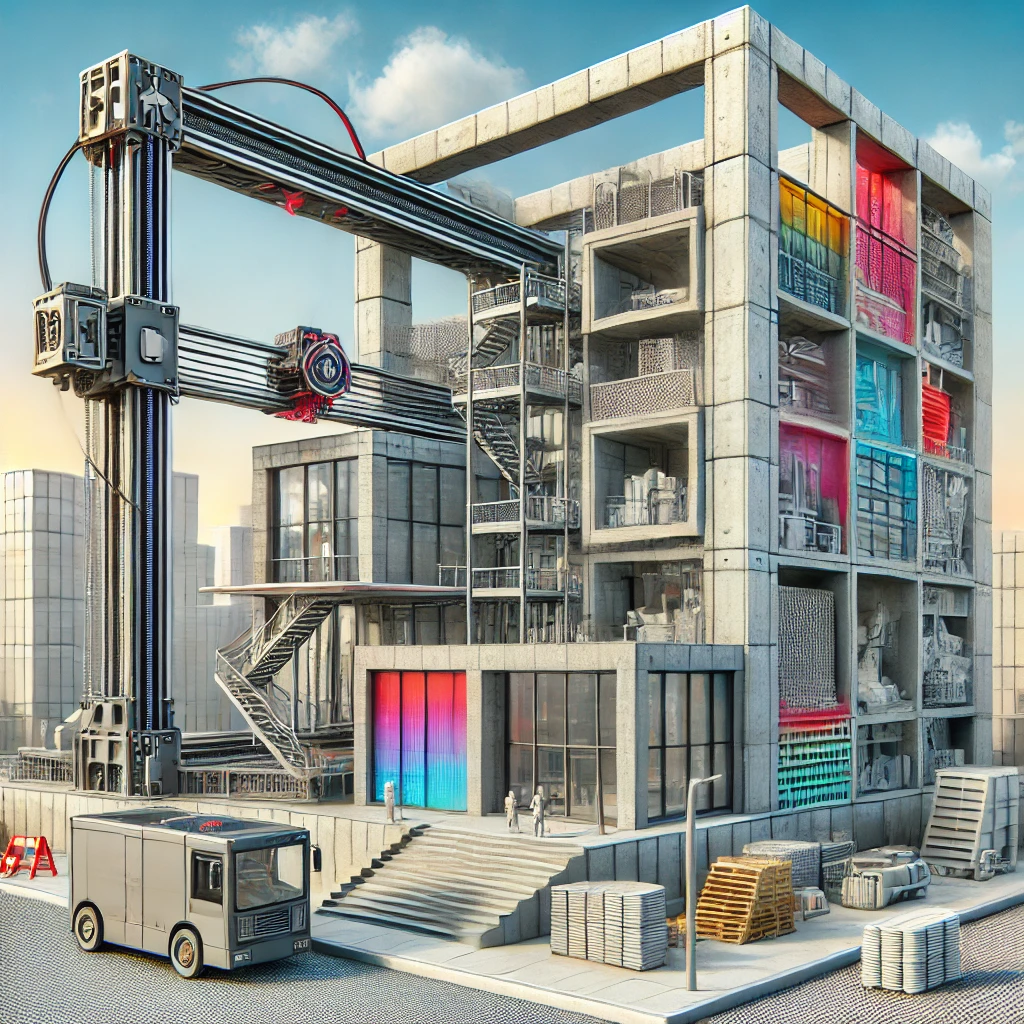
3D Printing in Engine Technology
India’s automotive and aerospace industries are increasingly exploring additive manufacturing for engine components. Traditional engine parts, which can be complex to manufacture, are now being produced with greater precision and less waste using 3D printing. For example, companies like Tata Motors and Mahindra have begun experimenting with 3D-printed engine components, which can reduce manufacturing time and material costs by up to 50%. Furthermore, these parts tend to be lighter and more durable, contributing to improved fuel efficiency and performance.
The Indian Space Research Organisation (ISRO) is also exploring the potential of 3D-printed components for rocket engines. By using this technology, they can produce highly intricate parts that withstand extreme temperatures and pressures, crucial for space missions. The faster production process enables ISRO to accelerate its mission timelines while cutting costs.
3D Printing in the Construction Sector
The Indian construction industry has long struggled with high costs, labor shortages, and slow project timelines. 3D printing is poised to transform this sector by offering faster, more cost-effective construction methods. In January 2023, IIT Madras, in collaboration with TVS Motor Company, unveiled India’s first 3D-printed house using concrete. The entire structure was printed in just five days, highlighting the speed advantage of this technology.
These houses are not only faster to construct but also cheaper, as 3D printing reduces material waste and labor costs. According to estimates, building a 3D-printed home in India could reduce costs by 30-40% compared to conventional methods. Furthermore, the technology allows for more sustainable construction, with potential applications in affordable housing, disaster relief, and rapid urbanization.
Global Adoption of 3D Printing
India is not alone in embracing Additive Manufacturing technology. Several countries have made significant strides in adopting 3D printing for both engine technology and construction:
- United States: The U.S. has been a leader in the development of 3D printing for aerospace and automotive industries. Companies like General Electric (GE) and Ford use 3D printing for engine components. The U.S. Army is even exploring 3D-printed barracks and operational bases to accelerate military infrastructure development.
- China: China has been at the forefront of using additive manufacturing for large-scale construction. In 2019, the country made headlines by constructing a 3D-printed office building in just 17 days. Moreover, China is also advancing its use of 3D printing in automotive engine technology.
- United Arab Emirates: The UAE has set an ambitious goal to have 25% of its buildings 3D-printed by 2030. Dubai has already made significant progress by completing the world’s largest 3D-printed building, a two-story structure measuring 6,900 square feet, within just a few weeks.
- Germany: Known for its engineering prowess, Germany has been a major player in the adoption of 3D printing for high-performance engine components, especially in the automotive and aviation sectors. Companies like BMW and Airbus have integrated 3D printing into their production processes to achieve more efficient and lighter components.
Speed and Cost Efficiency of 3D Printing
One of the main advantages of 3D printing is the speed at which products and buildings can be created. Traditional manufacturing processes for complex engine parts can take weeks or even months, whereas additive manufacturing can drastically reduce this to just a few days. Similarly, constructing a conventional building takes several months, while a 3D-printed house can be erected in a matter of days.
Cost is another key element that has made additive manufacturing attractive to industries and governments. For example, in the construction sector, a 3D-printed house in India could cost around ₹10-15 lakh ($13,000 – $19,000), whereas a conventionally built house of the same size could cost nearly twice as much. In terms of engine technology, the material savings, reduced labor costs, and shorter production cycles result in significant cost reductions for manufacturers.
Challenges and Future Prospects
Despite its advantages, 3D printing in India still faces certain challenges, such as the high initial setup costs, lack of skilled labor, and regulatory hurdles. However, with continued investment in research and development, and growing awareness of its potential, additive manufacturing could soon become a mainstream technology across multiple sectors.
India’s adoption of 3D printing marks an exciting shift towards innovation and sustainability. With its vast potential to revolutionize engine technology and the construction industry, the country is poised to leverage this technology for economic growth and societal development.